2016年我國汽車產(chǎn)銷量雙雙突破2800萬輛,連續(xù)第8年位居全球第一。隨著汽車工業(yè)的迅猛發(fā)展和業(yè)內(nèi)競爭加劇,行業(yè)內(nèi)對于汽車輕量化、低油耗、低成本、低污染、高安全性和高舒適性的要求愈加嚴格,新型材料的應用是發(fā)展的必然趨勢。

本世紀初,比利時Katholieke大學幾位研究人員提出了用紙蜂窩材料制造乘用車輕質(zhì)結(jié)構(gòu)板材的研發(fā)項目,此項目列入了歐盟的高科技EUREKA計劃,并得到了比利時政府的支持和資助,成功研發(fā)了以瓦楞芯紙結(jié)構(gòu)的乘用車結(jié)構(gòu)板材。荷力勝于2007年首先開始在國內(nèi)著手乘用車蜂窩結(jié)構(gòu)板材的研究,2008年申請了一個實用新型專利《一種轎車尾箱用載物墊》,2009年獲得國家知識產(chǎn)權(quán)局的授權(quán)。
正是由于在蜂窩材料領域的領先地位,以及在蜂窩結(jié)構(gòu)板材方面的不斷創(chuàng)新,荷力勝與廣州鴻力復合材料有限公司聯(lián)合申報的《乘用車蜂窩結(jié)構(gòu)板材的研發(fā)與大規(guī)模產(chǎn)業(yè)化》項目被列入了2012年的“廣東省高新區(qū)發(fā)展引導專項計劃”,獲得了廣東省政府的研發(fā)資金的資助,該項目在2013年底完成研發(fā),并開始了大規(guī)模的產(chǎn)業(yè)化推廣應用。
通過該項目的研發(fā),荷力勝研發(fā)出了高強度小孔徑蜂窩紙芯連續(xù)生產(chǎn)技術(shù)、工藝和裝備,而鴻力公司形成一套把紙蜂窩結(jié)構(gòu)材料與自然纖維或其它合成纖維材料復合成型的工藝、技術(shù)和裝備。此項新技術(shù)和新工藝除成功運用在乘用車內(nèi)部裝飾板材的生產(chǎn)外,還可以應用裝配式整體衛(wèi)生間和廚房產(chǎn)品,填補了國內(nèi)空白。2012年申請的《一種蜂窩復合板及其制造方法》發(fā)明專利以及其它幾項專利獲得了國家知識產(chǎn)權(quán)局的授權(quán)。
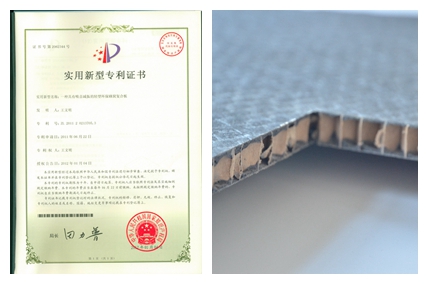
?在項目大規(guī)模產(chǎn)業(yè)化過程中,荷力勝于2013年在廣州建成了一條乘用車用高強度小孔徑蜂窩結(jié)構(gòu)材料生產(chǎn)線,形成了年產(chǎn)500 萬平方米乘用車用蜂窩材料生產(chǎn)能力,2014年又在荷力勝常熟分公司建成一條新的乘用車用蜂窩材料的生產(chǎn)線,將乘用車蜂窩材料的生產(chǎn)能力提升到1000萬平方米;而鴻力公司在產(chǎn)業(yè)化過程中利用研發(fā)出的新工藝和新技術(shù),成功地研發(fā)出全球首創(chuàng)的裝配式蜂窩復合板整體衛(wèi)生間和整體廚房產(chǎn)品,得到萬科等房地產(chǎn)企業(yè)的青睞。
蜂窩汽車板采用噴涂工藝將聚氨酯玻纖及荷力勝蜂窩紙芯復合成具有重量輕、彎曲強度大、尺寸穩(wěn)定性好、耐腐蝕、生產(chǎn)效率高、設計靈活等優(yōu)點的高輕度板材。和傳統(tǒng)材料相比,在同樣剛度條件下,其重量減輕了2/3以上,大大減輕了板材的重量,滿足乘用車輕量化的技術(shù)要求。
在汽車結(jié)構(gòu)中,蜂窩復合材料可應用于天窗、備胎蓋板、行李箱隔板、擱物板等多個部位,另外,該復合材料還可以廣泛應用在建筑裝飾、家具、運動器材等領域,是替代傳統(tǒng)環(huán)氧類和PP樹脂的理想之選。
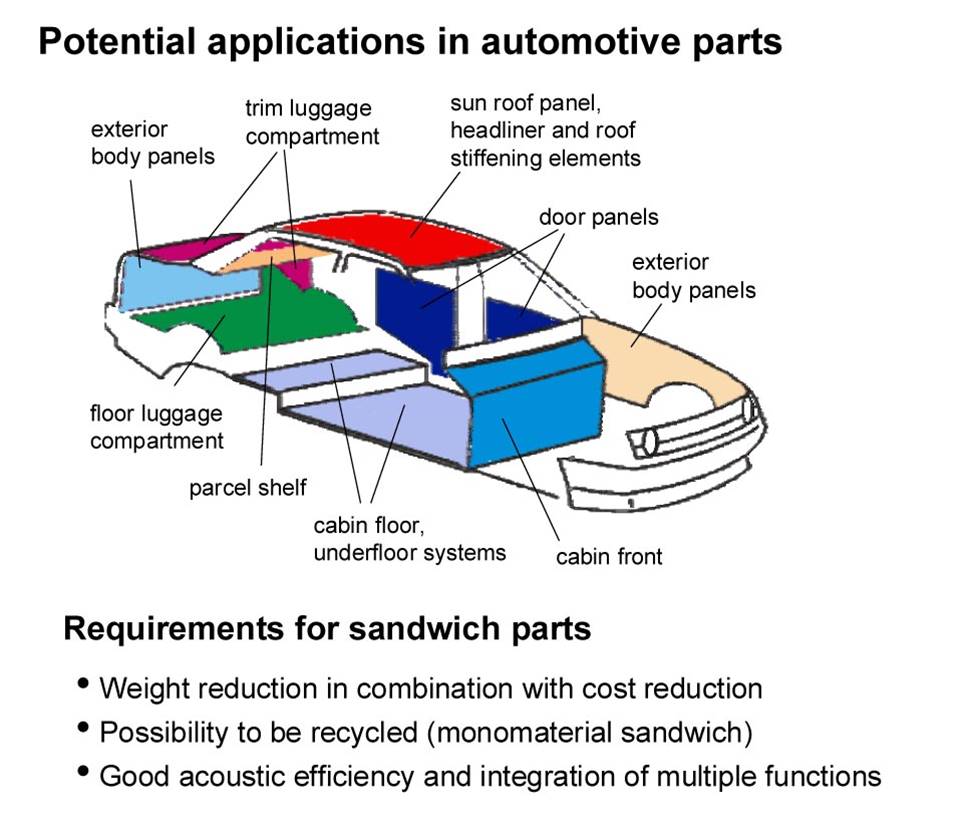
?
鑒于汽車蜂窩板強度高、重量輕的優(yōu)勢,從2013年開始,國內(nèi)乘用車的零部件供應商開始對乘用車用蜂窩板材進行評估,其輕質(zhì)高強度的特點很快獲得汽車廠商的青睞,佩爾哲、偉巴斯特、博信等國內(nèi)外知名汽車配件廠商均開始采用荷力勝蜂窩材料制成各種內(nèi)飾板材,供應如路虎、沃爾沃、福特、長安、哈弗等各型乘用車。
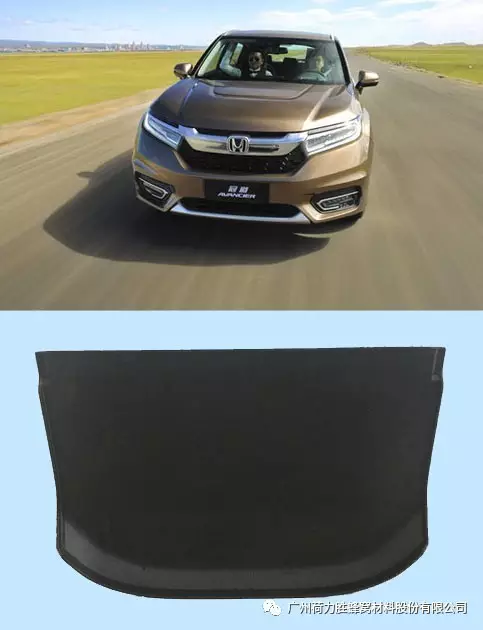
隨著消費者對車輛低油耗性能越來越看重,越來越多的汽車品牌選擇采用蜂窩汽車板來實現(xiàn)汽車輕量化,本田最新的中大型SUV冠道,在與競品車型相似的尺寸下,車身減重約200kg,隨之而來的,便是車輛更好的操控性及燃油經(jīng)濟性。
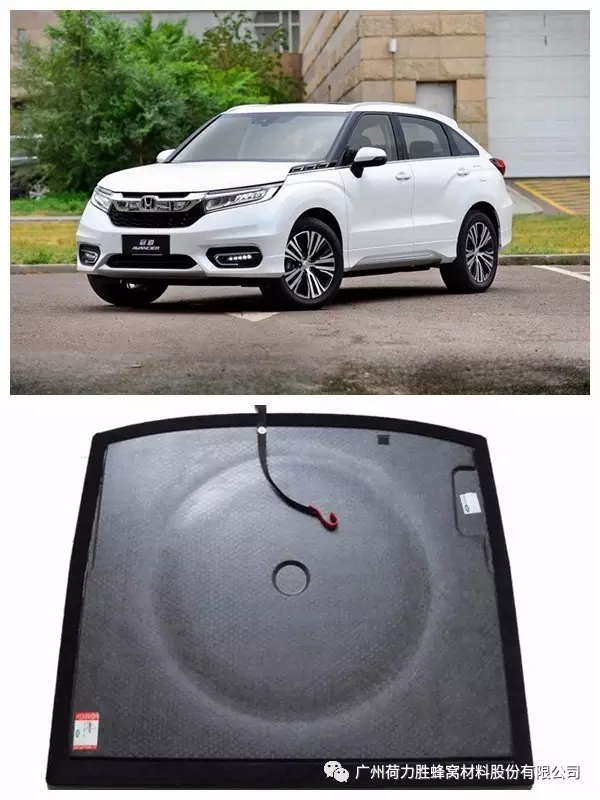
圖為路虎SUV及其采用荷力勝蜂窩材料的后尾箱隔板
荷力勝在蜂窩材料行業(yè)的不斷耕耘,為汽車的輕量化貢獻者自己的智慧,相信這一份執(zhí)著與專注,會為汽車輕量化及其他行業(yè)的進步帶來更多創(chuàng)新。